Over 100 Year History of Wiper Innovation
For over one hundred years, TRICO has engineered and manufactured premium wiper blades, bringing the latest innovations and original equipment rigor and quality to the wiper blade industry to keep you and your passengers safe with maximum visibility in all driving conditions.
Milestone Timeline
Directions: Select a timeframe to view TRICO milestones
1917 Rain rubber introduced.
First mass produced, commercially available wiper blade.
1921 Automatic vacuum wiper motor was introduced.
1923 Crescent cleaner offered.
1927 Visionall® two blade wiper system introduced.
1928 TRICO UK Established.
TRICO’s UK manufacturing plant in Brentford, England, opens.
1929 Dual Wipers.
This innovation marked the period when wiper blades began working in unison to improve visibility.
1921 Automatic vacuum wiper motor was introduced.







Manufacturing Excellence
Our research and manufacturing capabilities include virtually every component of a windscreen wiper/washer system, creating in the process a worldwide powerhouse capable of designing and manufacturing solutions for the vehicles of tomorrow, today.

The highest standards create the highest quality. TRICO's wiper industry leadership begins
at our 81,000-square-foot Global Technology Center in Rochester Hills, Michigan – the most
advanced of TRICO's development and test facilities around the globe. It is equipped
with the latest in analytical testing used in a grueling regimen that puts wiper systems
through harsher-than-real-world conditions for extended periods of time.
TRICO Rochester Hills Technology Center features:
- Validation laboratory – 45,000 square feet
- Staff 70 engineers at the Technology Center in Rochester Hills, Michigan, plus another 200 around the globe.
- House more than 60 test chambers, 150 test bucks and 6 full- size vehicle test bays for R&D
- 60+ CAD workstations using the latest in computer-aided design software technology
- Full warranty analysis and tear-down capability; warranty lessons learned are reviewed with all business units and manufacturing locations via TRICO CAS system
- TS 16949 certification, ISO 9001 and ISO 14001, Porsche VDA 6, plus many of the highest quality ratings from the world’s leading automakers.

With over 1,000 patented innovations, over 200 engineers across the globe, and TRICO’s strong,
enduring relationships with original equipment manufacturers fuels our knowledge, keeping us
at the forefront of the wiper industry and allowing us to be the first to bring innovative
solutions to the aftermarket. Every day, we partner with OEM experts to cultivate new ideas that
truly make a difference in wiper blade performance. Throughout the development process, our
products are put through harsher-than-real-world testing conditions at our R&D facility.
Our tools:
- KBE – enables wiper system design and integration in the vehicle-specific environment
- ADAMS
- FEA: Static and dynamic – performed to simulate conditions where systems are most likely to fail
- CFD: 2-D and 3-D
- Thermal FEA
- Magnetic FEA
- Proprietary Variflex beam blade design software
- Monthly review by each business unit for ongoing analysis of trends, claims and failures; summary reported in Monthly Quality Review with plant quality and management
- Weekly reviews of returned part analysis among design engineering, plant warranty group and plant quality
- Formalized Corrective Action System to address new issues

A focus on quality so drivers can focus on the road.

Trico Products ensures that quality improvement is continuous, effective and a pervasive theme throughout all business activity. The commitment and policy for quality are expressed in the KEY OBJECTIVES for quality:
- Provide best-in-class products and services
- Continuous improvement approach to all aspects of the business
- Motivate, train and educate all employees
- Provide an environment that supports teamwork and personal growth

TRICO’s quality program has been certified since 1995. The Management System standard requires, among other things:
- Understanding the organization and its context
- Understanding the needs and expectations of interested parties
- Identification of objectives and implemention of actions for improved performance
- A proactive management for quality impacts to the organization

As a world-class manufacturer of windshield wiper systems, TRICO is not only committed
to supplying the highest quality wiper products, but also to how our manufacturing processes
impact our employees and the environment. We have developed several internal policies and
annual goals to ensure that we always meet the highest standards.
Key highlights
- TRICO has its own waste water treatment facilities wherever the manufacturing or finishing processes involve contact water to ensure wastewater discharges comply with effluent limitations
- The use of plastic returnable containers for both interplant shipments and for final delivery to customers greatly reduces the amount of scrap wooden pallets, scrap cardboard, etc.
- Programs are in place to recycle all spent solvents and used oils/lubricants
- New program related to opportunity chargers for forklift batteries is expected to result in less energy consumption at time of battery recharge

TRICO is dedicated worldwide to providing a healthy, safe workplace and conducting its operations in an environmentally responsible manner. Our policy for the environmental management system is expressed through our commitment to:
- Compliance with all applicable laws, regulations and corporate initiatives
- Reducing environmental impact through prevention of pollution
- Setting and reviewing environmental objectives and targets
- Continual improvement of health, safety and environmental performance
We also have specific reduction goals related to energy consumption and waste generation, including:
- Hazardous waste minimization
- Recycling programs
- Electricity use
- Natural gas use
- Water use

- TRICO's EMS program has been certified to ISO 14001 since 2002
- TS16949
- ISO 9001
- Unsurpassed warranty performance
- World class PPM level – running below 10
- Identification of all environmental impacts and associated aspects
- Identification of environmental objectives and implement actions for improved performance
- A proactive management of the environmental impact of an organization
- Minimize how their operations negatively affect the environment
- Comply with applicable laws, regulations and other requirements
- Improve the environmental footprint of their operations
- They can trust that the company is actively minimizing their environmental impact
- There is proof that the company has been measured against best practice standards and found compliant


- “Big Idea” Award at Meijer Vendor Summit
- Outstanding Shipping Performance Award from Aftermarket Auto Parts Alliance, Inc
- General Motors Silver Supplier Award
- NAPA “Excellence in Quality” Vendor Award
- Advance Auto Parts “Supply Chain Reliability Vendor of the Year”
- MOPAR Quality Supplier of the Year
- Subaru of America Supplier Excellence Award
- A1 Product of the Year Award for TRICO Exact-Fit
- Chrysler Gold Pentastar
- Ford Q1 Preferred Supplier
- Porsche VDA 6
- Rover Group RG2000
- Volkswagen VDA
- Subaru Service of the Year
- Frost and Sullivan NeoForm® Beam Blade Industry Innovation Award
TRICO Quality Awards






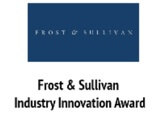